skip to main |
skip to sidebar
Calculating the Amount of Available Power
10:19 PM
Posted by Energetic
A simple formula for approximating electric power production at a hydroelectric plant is: P = ρhrgk, where
- P is Power in watts,
- ρ is the density of water (~1000 kg/m3),
- h is height in meters,
- r is flow rate in cubic meters per second,
- g is acceleration due to gravity of 9.8 m/s2,
- k is a coefficient of efficiency ranging from 0 to 1. Efficiency is often higher (that is, closer to 1) with larger and more modern turbines.
Annual electric energy production depends on the available water supply. In some installations the water flow rate can vary by a factor of 10:1 over the course of a year.
A hydropower resource can be measured according to the amount of available power, or energy per unit time. In large reservoirs, the available power is generally only a function of the hydraulic head and rate of fluid flow. In a reservoir, the head is the height of water in the reservoir relative to its height after discharge. Each unit of water can do an amount of work equal to its weight times the head.
The amount of energy, E, released when an object of mass m drops a height h in a gravitational field of strength g is given by
The energy available to hydroelectric dams is the energy that can be liberated by lowering water in a controlled way. In these situations, the power is related to the mass flow rate.
Substituting P for E⁄t and expressing m⁄t in terms of the volume of liquid moved per unit time (the rate of fluid flow, φ) and the density of water, we arrive at the usual form of this expression:
or
A simple formula for approximating electric power production at a hydroelectric plant is:
P = hrgk
where P is Power in kilowatts, h is height in meters, r is flow rate in cubic meters per second, g is acceleration due to gravity of 9.8 m/s2, and k is a coefficient of efficiency ranging from 0 to 1. Efficiency is often higher with larger and more modern turbines.
Some hydropower systems such as water wheels can draw power from the flow of a body of water without necessarily changing its height. In this case, the available power is the kinetic energy of the flowing water.
where v is the speed of the water, or with
where A is the area through which the water passes, also
Over-shot water wheels can efficiently capture both types of energy.
Pico Hydro
5:33 PM
Posted by Energetic
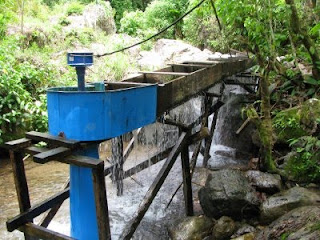
Pico hydro is a term used for hydroelectric power generation of under 5 kW. It is useful in small, remote communities that require only a small amount of electricity - for example, to power one or two fluorescent light bulbs and a TV or radio in 50 or so homes. Even smaller turbines of 200-300W may power a single home in a developing country with a drop of only 1 meter. Pico-hydro setups typically are run-of-stream, meaning that dams are not used, but rather pipes divert some of the flow, drop this down a gradient, and through the turbine before being exhausted back to the stream.
Like other hydroelectric and renewable source power generation, pollution and consumption of fossil fuels is reduced (there is still typically an environmental cost to the manufacture of the generator and distribution methods)
Turbine types
There are several different types of water turbine. Each type operates over a limited range of site conditions in terms of head and flow. Given a typical efficiency, a 1 kW scheme could acquire its energy from 200 m head with a flow rate of 1 litre/s or 2 m head with a flow rate of 100 l/s.
High Head Turbines
For higher head schemes, a Pelton turbine is the ideal choice. Pelton turbines use a jet of water which drives a runner with "buckets" which are specially shaped to capture as much energy as possible. This site has details of a particular layout of Pelton turbine, known as the Pico Power Pack, where the turbine is mounted on a shaft extension fitted to a standard induction motor used as a generator. The layout of the turbine, with a runner attached to a shaft extension from the horizontally-mounted generator, was developed through a synthesis of design ideas from two experienced manufacturers of micro and pico Pelton turbines – Akkal Man Nakarmi from Nepal and Mauricio Gnecco from Colombia. Bucket patterns for the Pico Power Pack are available for three sizes of runner.
Medium Head Turbines
Pumps as turbines are one option for sites with medium head, which have the advantage of being widely available and usually supplied with an induction motor that can be used as a generator. More information on these can be found on a dedicated Pumps as Turbines website.
Turgo turbines are a another good option for medium to high head schemes, with efficiencies of over 70% possible even for pico turbines. Crossflow (Mitchell-Banki) turbines are commonly used and are relatively easy to manufacture locally, e.g. in Indonesia (add link). However, for pico hydro they tend to be large in size and run at relatively slow speeds. Even for turbines with power of 10 kW, efficiencies of above 70% are difficult to obtain in the field although higher efficiencies have been reported from optimized laboratory turbines (add link [15]).
Low Head Turbine
There are a few different options for low head sites, including traditional water wheels (European type horizonal axis and Asian/South American type vertical axis). These tend to be large and to run slowly, but they have the advantage of allowing leaves and other matter to flow through without blockage.
There are also at least three types of water turbine - tube turbines (with axial guide vanes), open flume turbines and closed volute turbines. A joint project between Nottingham Trent University and Practical Action in Peru (funded by the Leverhulme Trust - 2004-07) has developed a closed volute design, which uses a scroll casing. The aim of this project was to produce a general design for pico propeller turbines and the results, which are described here, have been very encouraging. In particular, it was found that over 70% turbine efficiency can be achieved without the need for expensive materials or manufacture. However, care must be taken with the design of the turbine components and matching of the design parameters. A design guide will be published on this website shortly.
Manufacturers
Two examples of pico hydro power can be found in Kenya, in the towns of Kithamba and Thimba. These produce 1.1 kW and 2.2 kW, respectively. Local residents were trained to maintain the hydro schemes. The pico hydro sites in Kenya won Ashden Awards for Sustainable Energy.
In Vietnam, several Chinese manufacturers have sold pico-powerplants at prices as low as 20-70$ for a powerplant of 300-500W.
Sam Redfield of the Appropriate Infrastructure Development Group (AIDG) has developed a pico-hydro generator made from common PVC pipe and a modified Toyota alternator housed in a five gallon bucket. The generator was developed to provide power to communities without access to the electricity grid in developing countries. Envisioned as an energy source to charge cell phones, provide lighting and charge batteries, the generator is designed to be made by artisans with basic skills and can be built for less than US $150.00. The Toyota alternator used in the generator is converted to a permanent magnet alternator allowing it to generate power at low RPMs. The Five Gallon Bucket Hydroelectric Generator was the subject of a work group at the 2008 International Development Design Summit (IDDS) at the Massachusetts Institute of Technology.
Micro Hydro
5:28 PM
Posted by Energetic
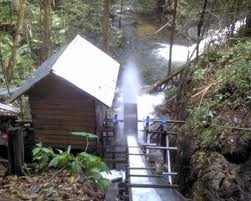
Micro hydro is a term used for hydroelectric power installations that typically produce up to 100 kW of power. These installations can provide power to an isolated home or small community, or are sometimes connected to electric power networks. There are many of these installations around the world, particularly in developing nations as they can provide an economical source of energy without purchase of fuel.
Micro hydro systems complement photovoltaic solar energy systems because in many areas, water flow, and thus available hydro power, is highest in the winter when solar energy is at a minimum.
Micro hydro is frequently accomplished with a pelton wheel for high head, low flow water supply. The installation is often just a small dammed pool, at the top of a waterfall, with several hundred feet of pipe leading to a small generator housing.
Construction & characteristics
Construction details of a microhydro plant are site-specific, but the common elements of all hydroelectric plants are present. A supply of water is needed — this can be a mountain stream, or a river. Usually microhydro installations do not have a dam and reservoir, relying on a minimal flow of water to be available year-round. Sometimes an existing mill-pond or other artificial reservoir is available and can be adapted for power production. An intake structure is required to screen out floating debris and fish, using a screen or array of bars to keep out large objects. In temperate climates this structure must resist ice as well. The intake may have a gate to allow the system to be dewatered for inspection and maintenance.
Water withdrawn from the source must move along a power canal or a pipe (penstock) to the turbine. If the water source and turbine are far apart, the construction of the penstock may be the largest part of the costs of construction. In mountainous areas, access to the route of the penstock may provide considerable challenges.
At the turbine, a controlling valve is installed to regulate the flow and the speed of the turbine. The turbine converts the flow and pressure of the water to mechanical energy; the water emerging from the turbine returns to the natural watercourse along a tailrace channel.
The turbine turns a generator, which is then connected to electrical loads; this might be directly connected to the power system of a single building in very small installations, or may be connected to a community distribution system for several homes or buildings.
Regulation & operation
Typically, an automatic controller operates the turbine inlet valve to maintain constant speed (and frequency) when the load changes on the generator. In a system connected to a grid with multiple sources, the turbine control ensures that power always flows out from the generator to the system. The frequency of the alternating current generated needs to match the local standard utility frequency. In some systems, if the useful load on the generator is not high enough, a load bank may be automatically connected to the generator to dissipate energy not required by the load; while this wastes energy, it may be required if its not possible to stop the water flow through the turbine.
An induction generator always operates at the grid frequency irrespective of its rotation speed; all that is necessary is to ensure that it is driven by the turbine faster than the synchronous speed so that it generates power rather than consuming it. Other types of generator require a speed control systems for frequency matching.
With the availability of modern power electronics it is often easier to operate the generator at an arbitrary frequency and feed its output through an inverter which produces output at grid frequency. Power electronics now allow the use of permanent magnet alternators that produce wild AC to be stabilised. This approach allows low speed / low head water turbines to be competitive; they can run at the best speed for extraction of energy, and the power frequency is controlled by the electronics instead of the generator.
Very small installations, a few kilowatts or smaller, may generate direct current and charge batteries for peak use times.
Turbine types used in Micro Hydro
Several different types of water turbines can be used in micro hydro installations, selection depending on the head of water, the volume of flow, and such factors as availability of local maintenance and transport of equipment to the site. For mountainous regions where a waterfall of 50 meters or more may be available, a Pelton wheel can be used. For low head installations, Francis or propeller-type turbines are used. Very low head installations of only a few meters may use propeller-type turbines in a pit. The very smallest micro hydro installations may successfully use industrial centrifugal pumps, run in reverse as prime movers; while the efficiency may not be as high as a purpose-built runner, the relatively low cost makes the projects economically feasible.
In low-head installations, maintenance and mechanism costs often become important. A low-head system moves larger amounts of water, and is more likely to encounter surface debris. For this reason a Banki turbine, a pressurized self-cleaning crossflow waterwheel, is often preferred for low-head microhydropower systems. Though less efficient, its simpler structure is less expensive than other low-head turbines of the same capacity. Since the water flows in, then out of it, it cleans itself and is less prone to jam with debris.
Two low-head schemes in England, Settle Hydro and Torrs Hydro use a reverse Archimedes' screw which is another debris-tolerant design. Other options include Gorlov, Francis and propeller turbines.
Another alternative is a large diameter, slow turning, permanent magnet, sloped open flow Kaplan turbine. A number of these have been installed at Trousy VLH, France
Small Hydro
4:53 PM
Posted by Energetic

Small hydro is the development of hydroelectric power on a scale serving a small community or industrial plant. The definition of a small hydro project varies but a generating capacity of up to 10 megawatts (MW) is generally accepted as the upper limit of what can be termed small hydro. This may be stretched up to 30 MW in the United States, and 50 MW in Canada. In contrast many hydroelectric projects are of enormous size, such as the generating plant at the Hoover Dam (2,074 megawatts) or the vast multiple projects of the Tennessee Valley Authority.
Small hydro can be further subdivided into mini hydro, usually defined as less than 1,000 kW, and micro hydro which is less than 100 kW. Micro hydro is usually the application of hydroelectric power sized for small communities, single families or small enterprise.
Small hydro plants may be connected to conventional electrical distribution networks as a source of low-cost renewable energy. Alternatively, small hydro projects may be built in isolated areas that would be uneconomic to serve from a network, or in areas where there is no national electrical distribution network. Since small hydro projects usually have minimal reservoirs and civil construction work, they are seen as having a relatively low environmental impact compared to large hydro. This decreased environmental impact depends strongly on the balance between stream flow and power production. One tool that helps evaluate this issue is the Flow Duration Curve or FDC. The FDC is a Pareto curve of a stream's daily flow rate vs. frequency. Reductions of diversion help the river's ecosystem, but reduce the hydro system's ROI. The hydro system designer and site developer must strike a balance to maintain both the health of the stream and the economics.
Generation of electric power
Hydroelectric power is the generation of electric power from the movement of water. A hydroelectric facility requires a dependable flow of water and a reasonable height of fall of water, called the head. In a typical installation, water is fed from a reservoir through a channel or pipe into a turbine. The pressure of the flowing water on the turbine blades causes the shaft to rotate. The rotating shaft is connected to an electrical generator which converts the motion of the shaft into electrical energy.
Small hydro is often developed using existing dams or through development of new dams whose primary purpose is river and lake water-level control, or irrigation. Occasionally old, abandoned hydro sites may be purchased and re-developed, sometimes salvaging substantial parts of the installation such as penstocks and turbines, or sometimes just re-using the water rights associated with an abandoned site. Either of these cost saving advantages can make the ROI for a small hydro site well worth the use of existing site infrastructure & water rights.
Project design
Many companies offer standardized turbine generator packages in the approximate size range of 200 kW to 10 MW. These "water to wire" packages simplify the planning and development of the site since one vendor looks after most of the equipment supply. Since non-recurring engineering costs are minimized and development cost is spread over multiple units, the cost of such systems is improved. While synchronous generators capable of isolated plant operation are often used, small hydro plants connected to an electrical grid system can use economical induction generators to further reduce installation cost and simplify control and operation.
Micro-hydro plants may use purpose-designed turbines or use industrial centrifugal pumps, connected in reverse to act as turbines. While these machines rarely have optimum hydraulic characteristics when operated as turbines, their low purchase cost makes them attractive for micro-hydro class installations.
Regulation of small hydro generating units may require diversion of water around the turbine, since the project may have no reservoir to store unused water. For micro-hydro schemes feeding only a few loads, a resistor bank may be used to dissipate electrical energy as heat during periods of low demand. In a sense this energy is wasted but the incremental fuel cost is negligible so there is little economic loss.
Other small hydro schemes may use tidal energy or propeller-type turbines immersed in flowing water to extract energy. Tidal schemes may require water storage or electrical energy storage to level out the intermittent (although exactly predictable) flow of power.
Since small hydro projects usually have minimal environmental and licensing procedures, and since the equipment is usually in serial production, standardized and simplified, and since the civil works construction is also small, small hydro projects may be developed very rapidly. The physically small size of equipment makes it easier to transport to remote areas without good road or rail access.
Micro-hydro installations can also provide multiple uses. For instance, micro-hydro projects in rural Asia have incorporated agro-processing facilities such as rice mills - alongside standard electrification - into the project design.
Sizes and Capacities of Hydroelectricity
4:27 PM
Posted by Energetic
Large and specialized industrial facilities
Although no official definition exist for the capacity range of large hydroelectric power stations, facilities from over a few hundred megawatts to more than 10 GW is generally considered large hydroelectric facilities. Currently, only three facilities over 10 GW (10,000 MW) are in operation worldwide; Three Gorges Dam at 22.5 GW, Itaipu Dam at 14 GW, and Guri Dam at 10.2 GW. Large-scale hydroelectric power stations are more commonly seen as the largest power producing facilities in the world, with some hydroelectric facilities capable of generating more than double the installed capacities of the current largest nuclear power stations.While many hydroelectric projects supply public electricity networks, some are created to serve specific industrial enterprises. Dedicated hydroelectric projects are often built to provide the substantial amounts of electricity needed for aluminium electrolytic plants, for example. The Grand Coulee Dam switched to support Alcoa aluminium in Bellingham, Washington, United States for American World War II airplanes before it was allowed to provide irrigation and power to citizens (in addition to aluminium power) after the war. In Suriname, the Brokopondo Reservoir was constructed to provide electricity for the Alcoa aluminium industry. New Zealand's Manapouri Power Station was constructed to supply electricity to the aluminium smelter at Tiwai Point.
The construction of these large hydroelectric facilities and the changes it makes to the environment, are often too at very large scales, creating just as much damage to the environment as at helps it by being a renewable resource. Many specialized organizations, such as the International Hydropower Association, look into these matters on a global scale.
Small
Small hydro is the development of hydroelectric power on a scale serving a small community or industrial plant. The definition of a small hydro project varies but a generating capacity of up to 10 megawatts (MW) is generally accepted as the upper limit of what can be termed small hydro. This may be stretched to 25 MW and 30 MW in Canada and the United States. Small-scale hydroelectricity production grew by 28% during 2008 from 2005, raising the total world small-hydro capacity to 85 GW. Over 70% of this was in China (65 GW), followed by Japan (3.5 GW), the United States (3 GW), and India (2 GW).
Small hydro plants may be connected to conventional electrical distribution networks as a source of low-cost renewable energy. Alternatively, small hydro projects may be built in isolated areas that would be uneconomic to serve from a network, or in areas where there is no national electrical distribution network. Since small hydro projects usually have minimal reservoirs and civil construction work, they are seen as having a relatively low environmental impact compared to large hydro. This decreased environmental impact depends strongly on the balance between stream flow and power production.
Micro Hydro
Micro hydro is a term used for hydroelectric power installations that typically produce up to 100 KW of power. These installations can provide power to an isolated home or small community, or are sometimes connected to electric power networks. There are many of these installations around the world, particularly in developing nations as they can provide an economical source of energy without purchase of fuel. Micro hydro systems complement photovoltaic solar energy systems because in many areas, water flow, and thus available hydro power, is highest in the winter when solar energy is at a minimum. Pico Hydro
Pico hydro is a term used for hydroelectric power generation of under 5 KW. It is useful in small, remote communities that require only a small amount of electricity. For example, to power one or two fluorescent light bulbs and a TV or radio for a few homes. Even smaller turbines of 200-300W may power a single home in a developing country with a drop of only 1 m (3 ft). Pico-hydro setups typically are run-of-the-river, meaning that dams are not used, but rather pipes divert some of the flow, drop this down a gradient, and through the turbine before being exhausted back to the stream.
Tidal Power Generating Methods of electricity
6:18 PM
Posted by Energetic

Tidal power, also called tidal energy, is a form of hydropower that converts the energy of tides into electricity or other useful forms of power. The first large-scale tidal power plant is Rance Tidal Power Station, started operation in 1966.
Although not yet widely used, tidal power has potential for future electricity generation. Tides are more predictable than wind energy and solar power. Among sources of renewable energy, tidal power has traditionally suffered from relatively high cost and limited availability of sites with sufficiently high tidal ranges or flow velocities, thus constricting its total availability. However, many recent technological developments and improvements, both in design (e.g. dynamic tidal power, tidal lagoons) and turbine technology (e.g. new axial turbines, cross-flow turbines), indicate that the total availability of tidal power may be much higher than previously assumed, and that economic and environmental costs may be brought down to competitive levels.
Historically, tide mills have been used, both in Europe and on the Atlantic coast of North America. The earliest occurrences date from the Middle Ages, or even from Roman times.Tidal power can be classified into three generating methods:
Tidal stream generator
Tidal stream generators (TSGs) make use of the kinetic energy of moving water to power turbines, in a similar way to wind turbines that use moving air. This method is gaining in popularity because of the lower cost and lower ecological impact compared to tidal barrages.
A tidal stream generator (TSG) is a machine that extracts energy from moving masses of water, or tides. These machines function very much like underwater wind turbines, hence are also sometimes referred to as tidal turbines.
TSGs are the cheapest and the least ecologically damaging among the three main forms of tidal power generation.Turbine power
Various turbine designs have varying efficiencies and therefore varying power output. If the efficiency of the turbine "ξ" is known the equation below can be used to determine the power output of a turbine.
The energy available from these kinetic systems can be expressed as:
where:
- ξ = the turbine efficiency
- P = the power generated (in watts)
- ρ = the density of the water (seawater is 1025 kg/m³)
- A = the sweep area of the turbine (in m²)
- V = the velocity of the flow
Relative to an open turbine in free stream, depending on the geometry of the shroud shrouded turbines are capable of as much as 3 to 4 times the power of the same turbine rotor in open flow.
Resource assessment
While initial assessments of the available energy in a channel have focus on calculations using the kinetic energy flux model, the limitations of tidal power generation are significantly more complicated. For example, the maximum physical possible energy extraction from a strait connecting two large basins is given to within 10% by:
where
- ρ = the density of the water (seawater is 1025 kg/m³)
- g = gravitational acceleration (9.81 m/s2)
- ΔHmax = maximum differential water surface elevation across the channel
- Qmax= maximum volumetric flow rate though the channel.
Tidal Barrage
Tidal barrages make use of the potential energy in the difference in height (or head) between high and low tides. Barrages are essentially dams across the full width of a tidal estuary, and suffer from very high civil infrastructure costs, a worldwide shortage of viable sites and environmental issues.
A Tidal barrage is a dam-like structure used to capture the energy from masses of water moving in and out of a bay or river due to tidal forces.
Instead of damming water on one side like a conventional dam, a tidal barrage first allows water to flow into the bay or river during high tide, and releasing the water back during low tide. This is done by measuring the tidal flow and controlling the sluice gates at key times of the tidal cycle. Turbines are then placed at these sluices to capture the energy as the water flows in and out.The barrage method of extracting tidal energy involves building a barrage across a bay or river that is subject to tidal flow. Turbines installed in the barrage wall generate power as water flows in and out of the estuary basin, bay, or river. These systems are similar to a hydro dam that produces Static Head or pressure head (a height of water pressure). When the water level outside of the basin or lagoon changes relative to the water level inside, the turbines are able to produce power.
The basic elements of a barrage are caissons, embankments, sluices, turbines, and ship locks. Sluices, turbines, and ship locks are housed in caissons (very large concrete blocks). Embankments seal a basin where it is not sealed by caissons.
The sluice gates applicable to tidal power are the flap gate, vertical rising gate, radial gate, and rising sector.
Only a few such plants exist. The largest is the Rance Tidal Power Station, on the Rance river, in France, which has been operating since 1966, and generates 240MW. Smaller plants include one on the Bay of Fundy, and another across a tiny inlet in Kislaya Guba, Russia). A number of proposals have been considered for a Severn barrage across the River Severn, from Brean Down in England to Lavernock Point near Cardiff in Wales.
Barrage systems are affected by problems of high civil infrastructure costs associated with what is in effect a dam being placed across estuarine systems, and the environmental problems associated with changing a large ecosystem.
Ebb generation
The basin is filled through the sluices until high tide. Then the sluice gates are closed. (At this stage there may be "Pumping" to raise the level further). The turbine gates are kept closed until the sea level falls to create sufficient head across the barrage, and then are opened so that the turbines generate until the head is again low. Then the sluices are opened, turbines disconnected and the basin is filled again. The cycle repeats itself. Ebb generation (also known as outflow generation) takes its name because generation occurs as the tide changes tidal direction.
Flood generation
The basin is filled through the turbines, which generate at tide flood. This is generally much less efficient than ebb generation, because the volume contained in the upper half of the basin (which is where ebb generation operates) is greater than the volume of the lower half (filled first during flood generation). Therefore the available level difference — important for the turbine power produced — between the basin side and the sea side of the barrage, reduces more quickly than it would in ebb generation. Rivers flowing into the basin may further reduce the energy potential, instead of enhancing it as in ebb generation. Of course this is not a problem with the "lagoon" model, without river inflow.
Pumping
Turbines are able to be powered in reverse by excess energy in the grid to increase the water level in the basin at high tide (for ebb generation). This energy is more than returned during generation, because power output is strongly related to the head. If water is raised 2 ft (61 cm) by pumping on a high tide of 10 ft (3 m), this will have been raised by 12 ft (3.7 m) at low tide. The cost of a 2 ft rise is returned by the benefits of a 12 ft rise. This is since the correlation between the potential energy is not a linear relationship, rather, is related by the square of the tidal height variation.
Two-basin schemes
Another form of energy barrage configuration is that of the dual basin type. With two basins, one is filled at high tide and the other is emptied at low tide. Turbines are placed between the basins. Two-basin schemes offer advantages over normal schemes in that generation time can be adjusted with high flexibility and it is also possible to generate almost continuously. In normal estuarine situations, however, two-basin schemes are very expensive to construct due to the cost of the extra length of barrage. There are some favourable geographies, however, which are well suited to this type of scheme.
Tidal lagoon power
Tidal pools are independent enclosing barrages built on high level tidal estuary land that trap the high water and release it to generate power, single pool, around 3.3W/m2. Two lagoons operating at different time intervals can guarantee continuous power output, around 4.5W/m2. Enhanced pumped storage tidal series of lagoons raises the water level higher than the high tide, and uses intermittant renewables for pumping, around 7.5W/m2. i.e. 10 x 10 km delivers 750MW constant output 24/7. These independent barages do not block the flow of the river and are a viable alternative to the Severn Barrage.
Energy calculations
The energy available from a barrage is dependent on the volume of water. The potential energy contained in a volume of water is:
where:
- h is the vertical tidal range,
- A is the horizontal area of the barrage basin,
- ρ is the density of water = 1025 kg per cubic meter (seawater varies between 1021 and 1030 kg per cubic meter) and
- g is the acceleration due to the Earth's gravity = 9.81 meters per second squared.
The factor half is due to the fact, that as the basin flows empty through the turbines, the hydraulic head over the dam reduces. The maximum head is only available at the moment of low water, assuming the high water level is still present in the basin.
Example calculation of tidal power generation
Assumptions:
- Let us assume that the tidal range of tide at a particular place is 32 feet = 10 m (approx)
- The surface of the tidal energy harnessing plant is 9 km² (3 km × 3 km)= 3000 m × 3000 m = 9 × 106 m2
- Density of sea water = 1025.18 kg/m3
Mass of the sea water = volume of sea water × density of sea water
-
- = (area × tidal range) of water × mass density
- = (9 × 106 m2 × 10 m) × 1025.18 kg/m3
- = 92 × 109 kg (approx)
Potential energy content of the water in the basin at high tide = ½ × area × density × gravitational acceleration × tidal range squared
-
- = ½ × 9 × 106 m2 × 1025 kg/m3 × 9.81 m/s2 × (10 m)2
- =4.5 × 1012 J (approx)
Now we have 2 high tides and 2 low tides every day. At low tide the potential energy is zero.
Therefore the total energy potential per day = Energy for a single high tide × 2
-
- = 4.5 × 1012 J × 2
- = 9 × 1012 J
Therefore, the mean power generation potential = Energy generation potential / time in 1 day
-
- = 9 × 1012 J / 86400 s
- = 104 MW
Assuming the power conversion efficiency to be 30%: The daily-average power generated = 104 MW * 30% / 100%
-
- = 31 MW (approx)
Because the available power varies with the square of the tidal range, a barrage is best placed in a location with very high-amplitude tides. Suitable locations are found in Russia, USA, Canada, Australia, Korea, the UK. Amplitudes of up to 17 m (56 ft) occur for example in the Bay of Fundy, where tidal resonance amplifies the tidal range.
Dynamic tidal power
Dynamic tidal power (or DTP) exploits an interaction between potential and kinetic energies in tidal flows. It proposes that very long dams (for example: 30–50 km length) be built from coasts straight out into the sea or ocean, without enclosing an area. Tidal phase differences are introduced by the dam, leading to a significant water level differential (at least 2–3 meters) in shallow coastal seas featuring strong coast-parallel oscillating tidal currents such as found in the UK, China and Korea. Each dam would generate power at a scale of 6 - 15 GW.
Dynamic tidal power or DTP is the newest technique of tidal power generation. It involves creating large dam-like structure extending from the coast straight to the ocean, with a perpendicular barrier at the far end, forming a large 'T' shape.
This long T-dam interferes with coast-parallel oscillating tidal waves which run along the coasts of continental shelves, containing powerful hydraulic currents (common in e.g. China, Korea, and the UK).
Run of the River Method: hydroelectricity generation
6:10 PM
Posted by Energetic

Run of the river hydroelectricity is a type of hydroelectric generation whereby the natural flow and elevation drop of a river are used to generate electricity. Power stations of this type are built on rivers with a consistent and steady flow, either natural or through the use of a large reservoir at the head of the river which then can provide a regulated steady flow for stations down-river.
The Concept of run of the river method
Advantages using run of the river method
Disadvantages using Run of the river method
The Concept of run of the river method
Run-of-river hydroelectricity is a type of hydroelectric generation whereby the natural flow and elevation drop of a river are used to generate electricity. Such projects divert some or most of a river’s flow (up to 95% of mean annual discharge) through a pipe and/or tunnel leading to electricity-generating turbines, then return the water back to the river downstream. A dam – smaller than used for traditional hydro – is required to ensure there is enough water to enter the “penstock” pipes that lead to the lower-elevation turbines.
Run-of-river projects are dramatically different in design and appearance from conventional hydroelectric projects. Traditional hydro dams store enormous quantities of water in reservoirs, necessitating the flooding of large tracts of land. In contrast, most run-of-river projects do not require a large impoundment of water, which is a key reason why such projects are often referred to as environmentally-friendly, or “green power.”
In recent years, many of the larger run-of-river projects have been designed to a scale and generating capacity rivaling some traditional hydro dams. For example, one run-of-river project currently proposed in British Columbia (BC) Canada – one of the world’s new epicenters of run-of-river development – has been designed to generate 1027 megawatts capacity.
Advantages using run of the river method
When developed with care to footprint size and location, run-of-river hydro projects can create sustainable green energy that minimizes impacts to the surrounding environment and nearby communities. Advantages include:
Cleaner Power, Less Greenhouse Gases
Like all hydro-electric power, run-of-river hydro harnesses the natural energy of water and gravity – eliminating the need to burn coal or natural gas to generate the electricity needed by consumers and industry.
Less Flooding/Reservoirs
Substantial flooding of the upper part of the river is not required for smaller-scale run-of-river projects as a large reservoir is not required. As a result, people living at or near the river don't need to be relocated and natural habitats and productive farmlands are not wiped out.
Disadvantages using Run of the river method
"Unfirm" Power
Run-of-River power is considered an “unfirm” source of power: a run-of-the-river project has little or no capacity for energy storage and hence can't co-ordinate the output of electricity generation to match consumer demand. It thus generates much more power during times when seasonal river flows are high (i.e, spring freshet), and much less during drier summer months.
Environmental Impacts
While small, well-sited run-of-river projects can be developed with minimal environmental impacts, many modern run-of-river projects are larger, with much more significant environmental concerns. For example, Plutonic Power Corp.’s Bute Inlet Hydroelectric Project in BC will see three clusters of run-of-river projects with 17 river diversions; as proposed, this run-of-river project will divert over 90 kilometres of streams and rivers into tunnels and pipelines, requiring 443 km of new transmission line, 267 km of permanent roads, and 142 bridges, to be built in wilderness areas.
British Columbia’s mountainous terrain and wealth of big rivers have made it a global testing ground for run-of-river technology. As of March 2010, there were 628 applications pending for new water licences solely for the purposes of power generation – representing more than 750 potential points of river diversion.
Many of the impacts of this technology are still not understood or well-considered, including the following:
- Diverting large amounts of river water reduce river flows affecting water velocity and depth, minimizing habitat quality for fish and aquatic organisms; reduced flows can lead to excessively warm water for salmon and other fish in summer. As planned, the Bute Inlet project in BC could divert 95 percent of the mean annual flow in at least three of the rivers).
- New access roads and transmission lines can cause extensive habitat fragmentation for many species, making inevitable the introduction of invasive species and increases in undesirable human activities, like illegal hunting.
- Cumulative impacts – the sum of impacts caused not only by the project, but by roads, transmission lines and all other nearby developments – are difficult to measure. Cumulative impacts are an especially important consideration in areas where projects are clustered in high densities close to sources of electricity demand: for example, of the 628 pending water license applications for hydro-power development in British Columbia, roughly one third are located in the south-western quarter of the province, where human population density and associated environmental impacts are highest.
- Water licenses – which are issued by the BC Ministry of Environment enabling developers to legally divert rivers – have not included clauses that specify changing water entitlements in response to altered conditions; this means that conflicts will arise over the water needed to both sustain aquatic life and generate power when river flow becomes more variable or decreases in the future.
Pumped-Storage Methods Hydroelectricity
5:28 PM
Posted by Energetic

Pumped-storage hydroelectricity is a type of hydroelectric power generation used by some power plants for load balancing. The method stores energy in the form of water, pumped from a lower elevation reservoir to a higher elevation. Low-cost off-peak electric power is used to run the pumps. During periods of high electrical demand, the stored water is released through turbines. Although the losses of the pumping process makes the plant a net consumer of energy overall, the system increases revenue by selling more electricity during periods of peak demand, when electricity prices are highest. Pumped storage is the largest-capacity form of grid energy storage now available.
Pumped Storage Hydroelectricity
At times of low electrical demand, excess generation capacity is used to pump water into the higher reservoir. When there is higher demand, water is released back into the lower reservoir through a turbine, generating electricity. Reversible turbine/generator assemblies act as pump and turbine (usually a Francis turbine design). Some facilities use abandoned mines as the lower reservoir, but many use the height difference between two natural bodies of water or artificial reservoirs. Pure pumped-storage plants just shift the water between reservoirs, but combined pump-storage plants also generate their own electricity like conventional hydroelectric plants through natural stream-flow. Plants that do not use pumped-storage are referred to as conventional hydroelectric plants; conventional hydroelectric plants that have significant storage capacity may be able to play a similar role in the electrical grid as pumped storage, by deferring output until needed.
Taking into account evaporation losses from the exposed water surface and conversion losses, approximately 70% to 85% of the electrical energy used to pump the water into the elevated reservoir can be regained. The technique is currently the most cost-effective means of storing large amounts of electrical energy on an operating basis, but capital costs and the presence of appropriate geography are critical decision factors.
The relatively low energy density of pumped storage systems requires either a very large body of water or a large variation in height. For example, 1000 kilograms of water (1 cubic meter) at the top of a 100 meter tower has a potential energy of about 0.272 kW·h (capable of raising the temperature of the same amount of water by only 0.23 Celsius = 0.42 Fahrenheit). The only way to store a significant amount of energy is by having a large body of water located on a hill relatively near, but as high as possible above, a second body of water. In some places this occurs naturally, in others one or both bodies of water have been man-made.
This system may be economical because it flattens out load variations on the power grid, permitting thermal power stations such as coal-fired plants and nuclear power plants and renewable energy power plants that provide base-load electricity to continue operating at peak efficiency (Base load power plants), while reducing the need for "peaking" power plants that use costly fuels. However, capital costs for purpose-built hydrostorage are high.
Along with energy management, pumped storage systems help control electrical network frequency and provide reserve generation. Thermal plants are much less able to respond to sudden changes in electrical demand, potentially causing frequency and voltage instability. Pumped storage plants, like other hydroelectric plants, can respond to load changes within seconds.
The first use of pumped storage was in the 1890s in Italy and Switzerland. In the 1930s reversible hydroelectric turbines became available. These turbines could operate as both turbine-generators and in reverse as electric motor driven pumps. The latest in large-scale engineering technology are variable speed machines for greater efficiency. These machines generate in synchronisation with the network frequency, but operate asynchronously (independent of the network frequency) as motor-pumps.
A new use for pumped storage is to level the fluctuating output of intermittent power sources. The pumped storage absorbs load at times of high output and low demand, while providing additional peak capacity. In certain jurisdictions, electricity prices may be close to zero or occasionally negative (Ontario in early September, 2006), indicating there is more generation than load available to absorb it; although at present this is rarely due to wind alone, increased wind generation may increase the likelihood of such occurrences. It is particularly likely that pumped storage will become especially important as a balance for very large scale photovoltaic generation.
Pumped Storage is Potential technologies
The use of underground reservoirs as lower dams has been investigated. Salt mines could be used, although ongoing and unwanted dissolution of salt could be a problem. If they prove affordable, underground systems might greatly expand the number of pumped storage sites. Saturated brine is about 20% more dense than fresh water.
A new concept is to use wind turbines or solar power to drive water pumps directly, in effect an 'Energy Storing Wind or Solar Dam'. This could provide a more efficient process and usefully smooth out the variability of energy captured from the wind or sun.
One can use pumped sea water to store the energy. A potential example of this could be used in a tidal barrage or tidal lagoon. A potential benefit of this arises if seawater is allowed to flow behind the barrage or into the lagoon at high tide when the water level is roughly equal either side of the barrier, when the potential energy difference is close to zero. Then water is released at low tide when a head of water has been built up behind the barrier, when there is a far greater potential energy difference between the two bodies of water. The result being that when the energy used to pump the water is recovered, it will have multiplied to a degree depending on the head of water built up. A further enhancement is to pump more water at high tide further increasing the head with for example intermittent renewable. Downsides: the generator must be below sea level, and marine organisms would tend to grow on the equipment and disrupt operation. This is not a major problem for the EDF La Rance Tidal power station in France.
Instead of pumping water uphill, the pumped storage idea can be inverted, pumping air under water.
Generating Methods of Hydroelectricity
5:15 PM
Posted by Energetic

There are four generating methods on hydroelectricity to generates power.
Conventional
Most hydroelectric power comes from the potential energy of dammed water driving a water turbine and generator. The power extracted from the water depends on the volume and on the difference in height between the source and the water's outflow. This height difference is called the head. The amount of potential energy in water is proportional to the head. To deliver water to a turbine while maintaining pressure arising from the head, a large pipe called a penstock may be used.
Pumped-storage
This method produces electricity to supply high peak demands by moving water between reservoirs at different elevations. At times of low electrical demand, excess generation capacity is used to pump water into the higher reservoir. When there is higher demand, water is released back into the lower reservoir through a turbine. Pumped-storage schemes currently provide the most commercially important means of large-scale grid energy storage and improve the daily capacity factor of the generation system.Run-of-the-river
Run-of-the-river hydroelectric stations are those with smaller reservoir capacities, thus making it impossible to store water.Tide
A tidal power plant makes use of the daily rise and fall of water due to tides; such sources are highly predictable, and if conditions permit construction of reservoirs, can also be dispatchable to generate power during high demand periods. Less common types of hydro schemes use water's kinetic energy or undammed sources such as undershot waterwheels.John Day Dam Hydroelectric Power
5:19 PM
Posted by Energetic

The John Day Dam Hydroelectric Power is a concrete gravity run-of-the-river dam spanning the Columbia River in the northwestern United States. The dam features a navigation lock plus fish ladders on both sides. The John Day Lock has the highest lift (110 feet) of any U.S. lock. The reservoir impounded by the dam is Lake Umatilla, and it runs 76.4 miles (123 kilometers) up the river channel to the foot of the McNary Dam. John Day Dam is part of the Columbia River Basin system of dams.
John Day Dam hydroelectric power plant is located 28 miles (45 km) east of the city of The Dalles, Oregon, and just below the mouth of the John Day River. The closest town on the Washington side is Goldendale, 20 miles (32 km) north. The closest town on the Oregon side is Rufus, Oregon. Its crest elevation is approximately 570 feet (170 m) above sea level. It joins Sherman County, Oregon with Klickitat County, Washington, 216 miles (348 kilometers) upriver from the mouth of the Columbia near Astoria, Oregon.
Construction of the John Day Dam Hydroelectric Power began in 1958 and was completed in 1971, making it the newest dam on the lower Columbia, at a total cost of US$511 million. John Day Dam was built and is operated by the U.S. Army Corps of Engineers. The dam's power generation capacity is 2,480,000 kW (overload capacity).
Specifications of John Day Dam
John Day Dam hydroelectric power plant is located 28 miles (45 km) east of the city of The Dalles, Oregon, and just below the mouth of the John Day River. The closest town on the Washington side is Goldendale, 20 miles (32 km) north. The closest town on the Oregon side is Rufus, Oregon. Its crest elevation is approximately 570 feet (170 m) above sea level. It joins Sherman County, Oregon with Klickitat County, Washington, 216 miles (348 kilometers) upriver from the mouth of the Columbia near Astoria, Oregon.
Construction of the John Day Dam Hydroelectric Power began in 1958 and was completed in 1971, making it the newest dam on the lower Columbia, at a total cost of US$511 million. John Day Dam was built and is operated by the U.S. Army Corps of Engineers. The dam's power generation capacity is 2,480,000 kW (overload capacity).
Specifications of John Day Dam
- Altitude: 266 feet (81 m) above sea level
- Height: 183 feet (56 m)
- Length: 7,365 feet (2,327 m)
- Navigation lock:
- Single-lift
- 86 feet (26 m) wide
- 675 feet (206 m) long
- Powerhouse
- Sixteen 135,000 kW units
- Total capacity: 2,160 MW
- Overload capacity: 2,485 MW
- Spillway
- Gates: 20
- Length: 1,228 feet (374 m)
John Day Dam | |
---|---|
Locale | Sherman County, Oregon / Klickitat County, Washington![]() |
Coordinates | ![]() |
Construction began | 1958 |
Opening date | 1971 |
Construction cost | US$511 million |
Dam and spillways | |
Type of dam | Concrete gravity, run-of-the-river |
Length | 2,327 m (7,635 ft) |
Height | 56 m (184 ft) |
Impounds | Columbia River |
Type of spillway | Service, gate-controlled |
Reservoir | |
Creates | Lake Umatilla |
Power station | |
Operator(s) | U.S. Army Corps of Engineers |
Type | Yes |
Turbines | 16 × 135 MW |
Installed capacity | 2,160 MW |
Maximum capacity | 2,485 MW |
Caruachi Hydroelectric Power
3:47 PM
Posted by Energetic

The Caruachi hydroelectric power facility is located on the Caroní River, in Bolivar state, Venezuela. The facility is located about 59 kilometers downstream from the Guri Dam belonging to the "Central Hidroeléctrica Simón Bolívar" and about 35 kilometres from where the Caroni and Orinoco Rivers meet at Ciudad Guayana.
Design and construction of Caruachi Hydroelectric Power
The Caruachi dam
The first of the 180 MW Kaplan turbine-generators General Electric supplied for the project began commercial operation in April 2003; the 12th and final unit entered service on February 28, 2006, and entered into formal/fully commercial operation on 31 March 2006, when the project was officially inaugurated.
Caruachi hydroelectric power installed capacity is 2,160 MW and the power plant will produce about 12 TW·h annually.
This project form jointly with the Central Hidroeléctrica Simón Bolívar in Guri, Antonio José de Sucre in Macagua and Manuel Piar in Tocoma (under construction), the development of Lower Caroní hydroelectric resources and one of the world's largest hydro projects now in construction, that, when completed, EDELCA (Electrificación del Caroní CA) claims will save Venezuela the equivalent of 750,000 barrels of oil per day, compared to 300,000 currently.
Design and construction of Caruachi Hydroelectric Power
The contract for the design, supply and installation of the main electro-mechanical equipment was awarded to a consortium of Kvaerner of Norway (Kvaerner's hydro interests since acquired by GE), GE Energy of America and Elin Transormatoren GmbH of Austria. Major work began on the project in 1998.
Following GE's acquisition of Kvaerner's hydro business in 1999, over 90% of the Caruachi contract was carried out by GE Hydro, including all aspects of the design, supply and installation of the turbines, generators, governors, exciters and cranes. The 180 MW Kaplan turbine-generators are among 12 GE Hydro units for the Caruachi project.
ABB won three contracts to provide the power transmission system for the project. A 400 kV substation and four related 400 kV transmission lines connect the plant with the country's transmission network.
Features
A main concrete 360 m gravity dam has a maximum height of 55 m from its foundations, with an integrated intake structure and powerhouse.
A 900 m right-abutment rockfill closure dam has a concrete slab face and a maximum height of 50 m, and a 4,200 m left-abutment earth and rockfill closure dam has a maximum height of 45 m.
A spillway with nine spans and radial surface gates has an aggregate 30,000 m³/s flow capacity.
A 470 m powerhouse is integrated with the main dam with space for 12 generating units (360 m) and an assembly bay (110 m).
Two transition dams have a 50 m intermediate buttress between the powerhouse and spillway. The 238 km² reservoir has a 91 m normal operating head.
Caruachi Dam | |
---|---|
Locale | Bolívar, ![]() |
Coordinates | ![]() |
Construction began | 1998 |
Opening date | 31 March 2006 |
Construction cost | US$2.1 billion |
Dam and spillways | |
Type of dam | Gravity dam |
Length | 360 m (1,181 ft) |
Height | 55 m (180 ft) |
Impounds | Caroni River |
Spillway capacity | 30,000 m3/s (1,100,000 cu ft/s) |
Reservoir | |
Creates | Caruachi Reservoir |
Surface area | 238 km2 (92 sq mi) |
Power station | |
Type | No |
Turbines | 12 × 180 MW |
Installed capacity | 2,160 MW |
Annual generation | 12,000 GWh |
Iron Gate I Hydroelectric Power Plant
1:39 PM
Posted by Energetic

The Iron Gate I Hydroelectric Power Plant is the largest dam on the Danube river and one of the largest hydro power plants in Europe. It is located on the Iron Gate gorge, between Romania and Serbia.
The Iron Gate I Hydroelectric Power Plant project started in 1964 as a joint-venture between the governments of Romania and Yugoslavia for the construction of a major dam on the Danube River which would serve both countries. At the time of completion in 1972, it was one of the largest hydroelectric power stations in the world with twelve units generating 2,052 MW, divided equally between the two countries at 1,026 MW each.
The Romanian part of the dam was modernized and the nominal capacity of the six units was increased from 175 MW to 194.4 MW, thus giving an installed capacity of 1,166 MW and increasing the entire power generation capacity of the dam to 2,192 MW. On the Serbian part of the dam, modernization started in July 2008 and is still in progress; so far Unit 6 has been modernized, and revitalization of the remaining five is in the preparation phase. The units are being upgraded with the help of Russian company ОАО "Рязанский станкостроительный завод" (Ryazan Machine Tool Plant), as well as their subcontractors with the participation of eleven domestic companies. The Romanian side of the power station produces approximately 5.4 TWh annually, while the Serbian side of the power station produces 5.65 TWh.
The discrepancy in power output between the two halves is due to the generating equipment. While Romania's equipment is newer and thus more efficient (thereby generating more power), it is proving more unreliable; resulting in increased downtime for maintenance/repairs, and consequently lower annual power output overall.
In addition to the upgrades, the Serbian side is planning on building a new, smaller power station, called Iron Gate III.ron Gate I Hydroelectric Power Station | |
---|---|
Locale | Iron Gate![]() ![]() |
Coordinates | ![]() |
Construction began | 1964 |
Opening date | 1972 |
Dam and spillways | |
Length | 1,278 m (4,193 ft) |
Height | 60 m (200 ft) |
Impounds | Danube River |
Reservoir | |
Creates | Iron Gate I Reservoir |
Capacity | 2.1 km3 (0.50 cu mi) |
Catchment area | 577,250 km2 (222,880 sq mi) |
Surface area | 104.41 km2 (40.31 sq mi) |
Power station | |
Turbines | Romania: 6 × 194.4 MW Serbia: 6 × 172 MW |
Installed capacity | 2,192 MW |
Annual generation | Romania: 5.4 TWh Serbia: 5.65 TWh |
Volga Hydroelectric Station
1:20 PM
Posted by Energetic
The Volga Hydroelectric Station or Volga GES (Russian: Волжская ГЭС) also known as the 22nd Congress of the CPSU Stalingrad/Volgograd Hydroelectric Power Station, is the largest hydroelectric station in Europe and is the last of the Volga-Kama Cascade of dams, before the Volga River flows into the Caspian Sea. Today, it is operated by the electricity company RusHydro.
Today the Volga Hydroelectric Station is the largest in Europe. Volgograd Hydroelectric Power Station consists of a 725-metre long, 44-metre high concrete dam that crosses the Volga river. Supporting it is a 3250-metre long landfilled dam with a maximum height of 47 metres. The Station also offers railway and road crossings of the Volga.
The present power rating of the station is 2,582.5 MW and annual energy output of 12.3 billion KW-hours. There are a total of 22 generators. 17 generators produce 115 MW each (four of which have recently received repairs and overhauls), three produce 125.5 MW each and two produce 120 MW. Three fishery paths drive additional 11 MW units each, but at present two are not functioning. Thus the initial output is slightly downrated.
The 4.9 kilometre dam forms the Volgograd reservoir. At present the station is managed by OAO Volzhskaya GES that is owned by OAO GidroOGK, a daughter company of the state organisation RAO AES Rossii.
The generators of the Volga Hydroelectric Station are connected to the power grid in a somewhat unusual way as the machine transformers of the generators serve also as inverter transformers of the static inverter plant of HVDC Volgograd-Donbass, which is situated on the dam. In opposite to other static inverter plants, it has no harmonic filters.
Volga Hydroelectric Power Station | |
---|---|
Official name | Волжская ГЭС |
Locale | Volga, ![]() |
Coordinates | ![]() |
Construction began | 6 August 1950 |
Opening date | 10 September 1961 |
Dam and spillways | |
Length | 725 m (2,379 ft) |
Height | 44 m (144 ft) |
Impounds | Volga River |
Reservoir | |
Creates | Volgograd Reservoir |
Capacity | 31.5 km3 (8 cu mi) |
Surface area | 3,117 km2 (1,203 sq mi) |
Power station | |
Type | No |
Turbines | 17 × 115.0 MW 03 × 125.5 MW 02 × 120.0 MW 03 × 011.0 MW |
Installed capacity | 2,582.5 MW |
Maximum capacity | 2,604.5 MW |
Annual generation | 12,300 GWh |
Atatürk Dam Hydroelectric Power Plant
2:18 AM
Posted by Energetic

The Atatürk Dam (Atatürk Barajı), originally the Karababa Dam, is a zoned rock-fill dam with a central core on the Euphrates River on the border of Adıyaman Province and Şanlıurfa Province in Southeastern Anatolia Region of Turkey. Built both to generate electricity and to irrigate the plains in the region, it is later renamed after Mustafa Kemal Atatürk (1881–1938), the founder of the Turkish Republic, to honor him with its very large scale. The construction began in 1983 and was completed in 1990. The dam and the hydroelectric power plant, which went into service after the upfilling of reservoir was accomplished in 1992, are operated by the State Hydraulic Works (DSİ). The reservoir created behind the dam, called Lake Atatürk Dam (Atatürk Baraj Gölü), is the third largest in Turkey.
The Atatürk Dam is situated at 24 km (15 mi) northwest to Bozova town of Şanlıurfa Province on the state road to Adıyaman. Centerpiece of the 22 dams on the Euphrates and the Tigris, which all form the integrated, multi-sector regional development project of Southeastern Anatolia Project, known as GAP, it is one of the world's largest dams. The Atatürk Dam, one of the five operational dams on the Euphrates as of 2008, is preceded by Keban and Karakaya dams upstream and followed by Birecik and the Karkamış dams downstream. Two more dams on the river are under construction.
The Atatürk Dam embankment is 169 m (554 ft) high and 1,820 m (5,970 ft) long. The hydroelectric power plant has a total installed power capacity of 2,400 MW generating 8,900 GWh electricity annually. The total cost of the dam project amounted about US$ 1.25 billion.
The Atatürk Dam was depicted on the reverse of the Turkish one million lira banknotes of 1995-2005 and of the 1 new lira banknote of 2005-2009.The Hydro-electric Power Plant of the Atatürk Dam is the biggest of a series of 19 power plants of the GAP project. It consists of eight Francis turbine and generator groups of 300 MW each, supplied by Sulzer Escher Wyss and ABB Asea Brown Boveri respectively. The up to 7,25 m dia steel pressure pipes (penstocks) with a total weight of 26.600 tons were supplied and installed by the German NOELL company (today DSD NOELL). The power plant's first two power units came on line in 1992 and it became fully operational in December 1993. The Hydro-electric Power Plant can generate 8,900 GWh of electricity annually. Its capacity makes up around one third of the total capacity of the GAP project.
During the periods of low demand for electricity, only one of the eight units of the Hydro-electric Power Plant is in operation while in times of high demand, all the eight units are in operation. Hence, depending upon the energy demand and the state of the interconnected system, the amount of water to be released from the Hydro-electric Power Plant might vary between 200 and 2,000 m³/sec in one day.
Subscribe to:
Posts (Atom)